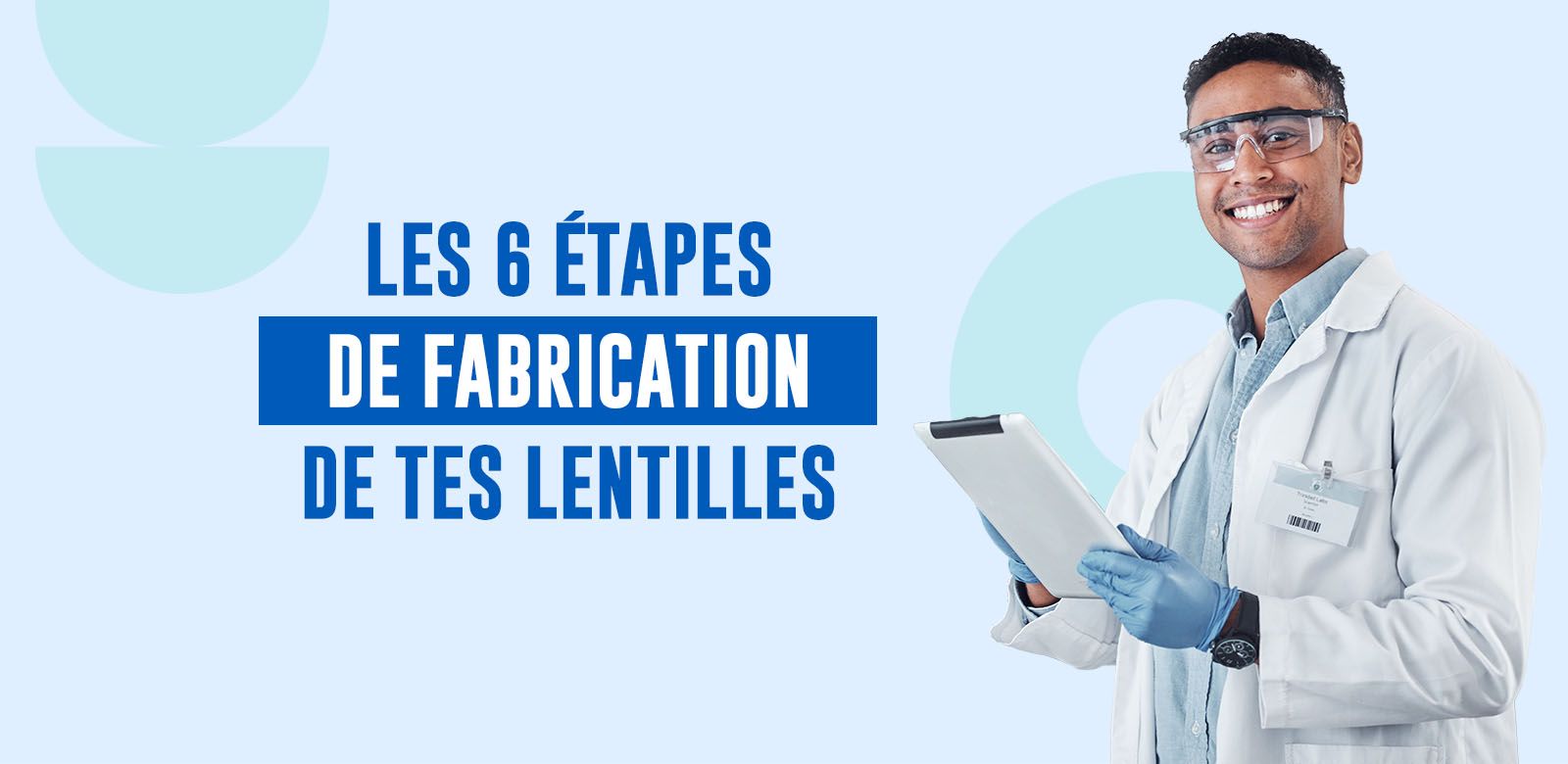
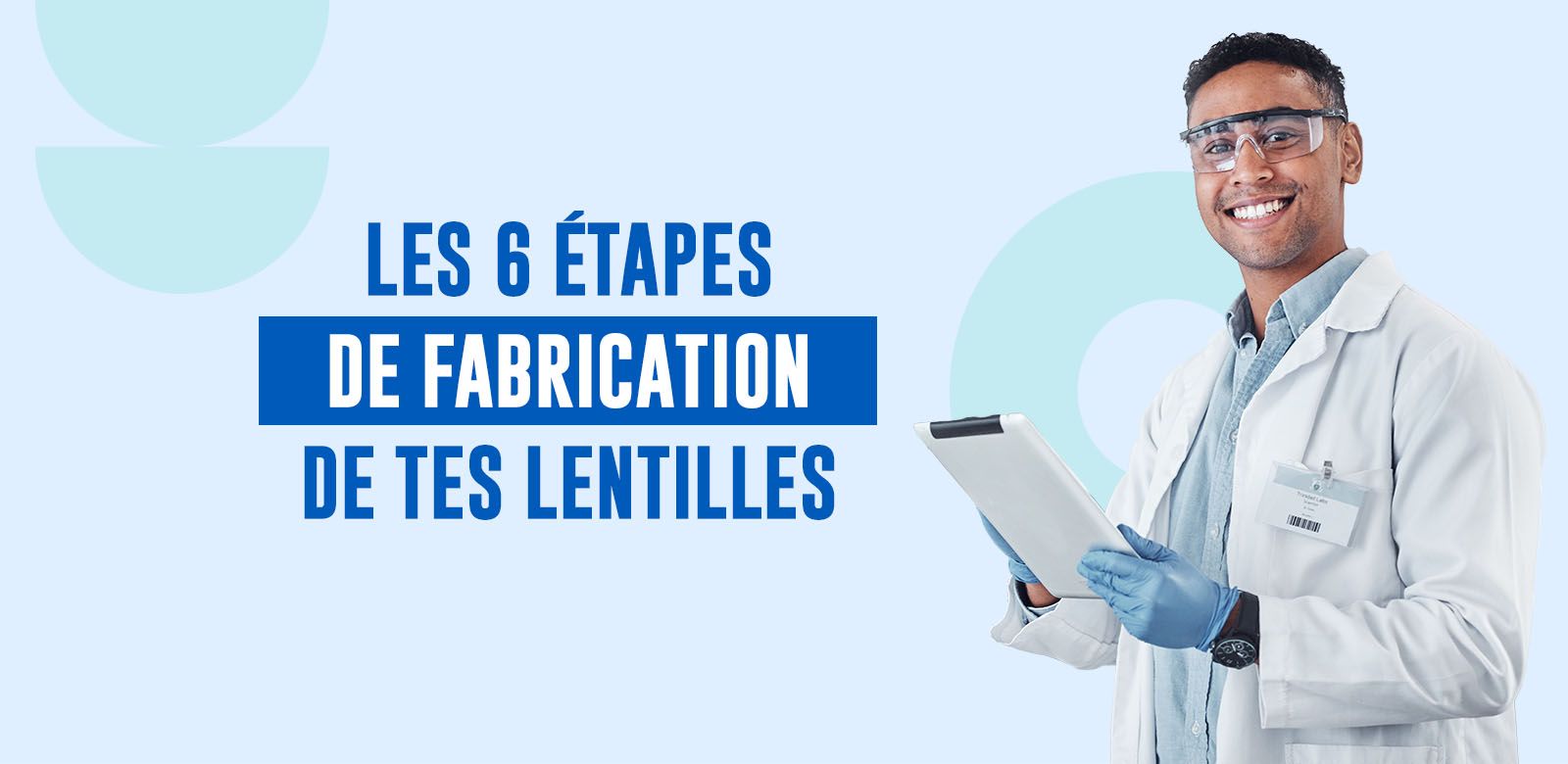
Sais-tu comment tes lentilles, si essentielles pour corriger les troubles de la vue tels que la myopie, l’astigmatisme et la presbytie, sont fabriquées ? Derrière chaque paire se cache un processus complexe et détaillé. Cet article te dévoilera les coulisses de leur fabrication, du design initial à la conception du moulage, en passant par les contrôles qualité, dans le but de te fournir les lentilles adaptées à tes besoins, tout en t’offrant un confort de port.
1ère étape : la sélection des matières premières
La première étape lors de la conception des lentilles de contact est de définir quelle matière première utiliser. La majorité sont fabriquées à partir d’un composant en plastique, similaire à de l’eau, spécialement conçu pour être compatible avec les yeux. Les deux principaux matériaux utilisés sont : l’hydrogel (également appelé hydrophile) et le silicone hydrogel.
-
Lentilles de contact en hydrogel : Elles s’adaptent à la forme de l’œil et ont une teneur en eau naturellement élevée, permettant une hydratation et un confort tout au long de la journée. On reconnaît les lentilles en hydrogel car elles se durcissent lorsqu’elles sèchent et redeviennent douces et souples quand elles sont hydratées. Cette technologie est souvent utilisée pour les lentilles souples, telles que les Dailies Aqua Comfort Plus ou les Biomedics 55 Evolution.
-
Lentilles de contact en silicone hydrogel : La principale différence avec les lentilles en hydrogel, c’est que celles en silicone hydrogel, telles que les lentilles mensuelles AirOptix Plus HydraGlyde ou les Total 30, offrent une perméabilité à l’oxygène élevée (quantité d’oxygène capable de traverser la lentille pour aller dans l’œil). Cela améliore considérablement le confort de port, tout au long de la journée.
2ème étape : la conception et le moulage
La création du moule
Dès que la matière première a été définie, on peut passer à l’étape suivante : la création du moule de la lentille. Ce moule est essentiel pour garantir que chaque modèle produit est unique et conforme aux spécifications définies (confort et vision optimale).
-
Conception du moule : Les ingénieurs vont commencer par dessiner la lentille à l’aide d’un logiciel de conception assistée par ordinateur (CAO), afin de définir ses dimensions et sa forme.
-
Fabrication du moule : Une fois le design finalisé, le moule est fabriqué à l'aide de machines de précision telles que des fraiseuses et des machines de découpe laser. Ces deux techniques assurent une précision micrométrique, cruciale pour offrir la meilleure qualité.
Le moulage
Une fois le moule créé, on peut passer à l'étape suivante : le moulage des lentilles de contact. Ce processus transforme la matière première brute en lentilles.
3ème étape : le polissage
Dès qu’elles ont été moulées, elles passent à l’étape du polissage. Cette étape sert à rendre la surface de la lentille lisse et douce.
4ème étape : le contrôle qualité
Elles passent ensuite par une série de contrôles qualité très rigoureux afin de s'assurer qu'elles répondent bien aux normes de sécurité et de performance.
Il existe deux types de vérifications : l’inspection optique et l’inspection mécanique. La première vérification va s’assurer de la clarté, de la forme et de l’aspect esthétique du modèle, tandis que la deuxième a pour but de vérifier leur résistance et leur durabilité.
5ème étape : la stérilisation et l’emballage
Une fois les lentilles fabriquées et polies, elles doivent être stérilisées pour éliminer tout risque de contamination. Après la stérilisation, elles sont emballées hermétiquement dans des solutions de stockage pour maintenir leur hydratation et leur stérilité.
6ème étape : la commercialisation
Dès que les lentilles ont bien été polies, qu’elles ont passé les contrôles qualité et qu’elles sont emballées hermétiquement, les fournisseurs peuvent commencer la commercialisation de leurs produits et les vendre aux différents revendeurs tels que Linsenmax, le spécialiste des lentilles de contact en Suisse depuis 2007.